Introduction
With recent developments in environmental regulations and the growing focus on carbon reduction, industries may want to consider Carbon Capture and Storage (CCS) as a viable solution to reduce their carbon emissions and take full advantage of available tax credits. This article explores the various methods of CCS, highlights the impurities that can impact its effectiveness, and emphasizes the importance of precise monitoring.
New Regulations on the Horizon
On Thursday, May 11, 2023, the EPA proposed new carbon standards for coal and natural gas-fired power plants. This rule differs significantly in approach from the past proposal to limit CO2 under the Obama administration, known as the Clean Power Plan (CPP), which focused more on shifting the energy sector to renewables rather than providing emission reduction pathways for the fossil fuel industry. EPA Administrator Michael Regan has said that he is confident that this new proposal will hold up better in the courts than the EPA’s 2015 proposal. As regulatory frameworks continue to evolve, industrial facilities may want to consider CCS to achieve emission reduction goals effectively.
CSS technology appears to be the most promising way to remove large amounts of carbon from the atmosphere, and it has gained significant attention in recent years. The process involves separating CO2 from other gases, compressing it into a liquid, and storing it in underground locations such as dry saline aquifers, dry oil reservoirs, or coal beds. Three different categories of technologies can be used to capture carbon at the source: post-combustion carbon capture (the most common in existing power plants), pre-combustion carbon capture (largely used in industrial processes), and oxy-fuel combustion systems.
Alternatively, captured carbon can be re-used in industrial processes by converting it into plastics, concrete, or biofuel–this is known as CCUS: Carbon Capture, Utilization, and Storage. For instance, CO2 can be stored as calcium carbonate through a process called “calcium looping”, or as solid carbon by a reaction of CO2 using a liquid metal catalyst. Stored carbon may also be injected into an oil field in a process known as enhanced oil recovery. However, the latter method tends to produce more carbon when the resulting oil is burned, making it less helpful in offsetting emissions. A more promising pathway for carbon reuse may be its potential as a component in future building materials.
Impurities: Hindrances to Effective CCS
While CCS holds immense potential, impurities present in CO2 streams pose challenges to its long-term viability. Contaminants in untreated process gases such as sulfur dioxide (SO2), nitrogen oxides (NOx), oxygen (O2), water vapor (H2O), methane (CH4), argon (Ar), and particulate matter can compromise the efficacy and longevity of CCS equipment. Lingering presence of these impurities in the resulting CO2 stream can induce corrosive reactions, drive unwanted microbial activity, reduce storage capacity, and impact the transport of CO2 through pipelines.
It is still uncertain what quantities of impurities are acceptable in carbon storage. This graph based on data from a study by Murugan et al. (2020) represents the possible maximum levels of a variety of CO2 impurities that could be present in gases captured from a variety of processes being considered for CCS.
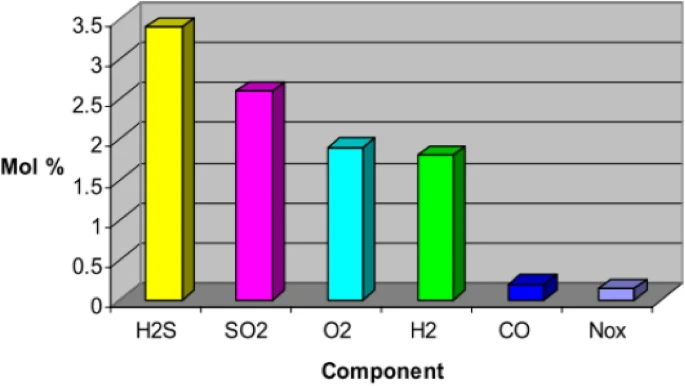
Figure 1. Possible maximum levels of a variety of CO2 impurities from industrial processes being considered for CCS (Razak et al, 2023 derived from Murugan et al. 2020).
To ensure optimal CCS performance, operators must be on the lookout for impurities. Excessive oxygen levels in CO2 storage (more than 100 ppm) can stimulate microbial activity leading to the production of hydrogen sulfide (H2S) and higher concentrations may pose a fire hazard. Concentrations of water vapor in the stream should be kept as low as possible, as it can generate acids, like sulfuric acid, that corrode pipelines. It can also form hydrates in the system that adhere to pipeline walls, causing blockages. The presence of excessive carbon monoxide (CO) (more than 5000 ppm) can hinder Enhanced Oil Recovery (EOR) performance. Dry air gases, including O2, N2, and Ar, can lower CO2 stream density, making storage more challenging. These are problematic in amounts greater than 10 ppm. Sulfur oxides (SOX) and H2S should be kept under 50 ppm due to their corrosive nature.
Nearly all combustion sources can create impure carbon emissions; the extent of impurities may vary according to the fuel that is burned. To remedy this, facilities may want to consider pre-combustion carbon capture or oxy-fuel combustion systems, which produce purer flue gas streams than typical post-combustion capture. In pre-combustion capture, the fuel is converted into a synthesis gas before it is burned, creating a relatively pure stream of CO2. Oxy-fuel combustion systems burn the fuel in an oxygen-rich environment rather than regular air, which leads to a flue gas of CO2 and water that contains less impurities.
The presence of some compounds in a flue gas stream can significantly impact the efficiency of amine scrubbing, a method of carbon capture that has been used for decades. Impurities can compete with CO2 for absorption sites on the amine solvent, reducing its scrubbing capacity. O2, NOX, SOX, and fly ash can degrade the amine solvent and cause foaming and corrosion of equipment and pipelines, leading to operational issues. Inert gases like nitrogen and oxygen in the gas stream can increase energy consumption during regeneration of the amine solvent, which can greatly increase operating costs. Mitigation of impurities can make amine scrubbing more efficient and cost-effective.
As post-combustion carbon capture technology like amine scrubbing becomes more widely adopted, emissions from this process might also become a concern for regulators. Facilities may also wish to monitor these emissions. Besides contributing to the pool of atmospheric nitrogen, release of amines and their degradation products can create continued reactions in the atmosphere, leading to the formation of carcinogenic compounds such as nitrosamines.
Two other problems arise from impurities in the transport and storage of a CO2 gas stream after it has been separated from the flue gas. In transport, even the slightest presence of impurities can change the phase behavior of the CO2 stream in a pipeline. Pipeline operators may have to respond by increasing the supply pressure to avoid hindering the system.
In storage, CO2 impurities reduce the storage capacity of a given space. Injection wells can fill earlier than expected when injected with impure CO2, inducing costs later. If impurities such as H2S and SOX react with water, the resulting corrosive acids can dissolve caprock in storage reservoirs, increasing the chances of a leak. The effects of CO2 leaks from pipelines and reservoirs on local populations is still not fully understood, but recent leaks have received significant media attention, such as one in Satartia, Mississippi in 2020 that hospitalized 45 people. Thus, facilities that store clean CO2 promote safety and may even avoid the headache of a lawsuit in the long term.
The Role of Measurement and Monitoring
Accurate measurement and monitoring of impurities are paramount to the widespread success of CCS. By precisely metering CO2 flow and quantifying impurity levels, companies can enhance carbon storage capacity, ensure safety, and avoid unforeseen expenses.
As a leading provider of measurement and monitoring services, CleanAir is positioned to help our clients navigate the field of carbon capture and storage and detect impurities in their gas streams. With our advanced analytical techniques, including Fourier Transform Infrared Spectroscopy (FTIR) and Gas Chromatography (GC), we offer clients unparalleled accuracy in detecting and quantifying impurities in both flue gas and CO2 streams.
For clients wanting to understand the composition of their flue gas, our FTIR technology provides a comprehensive analysis of the infrared absorption spectrum, enabling the identification of compounds with acute sensitivity. By comparing the sample spectrum to reference baselines, this technology can detect even trace amounts of problematic compounds in flue gas, from volatile organic compounds to nitrogen oxides and sulfur compounds.
Our GC systems offer precise impurity analysis in a CO2 gas stream. With their ability to separate complex mixtures into individual components, our GC instruments precisely quantify impurities, guaranteeing an in-depth understanding of any CO2 stream’s composition.
Conclusion
At CleanAir, we go beyond accurate measurement. Our team of expert scientists and engineers works closely with clients to develop personalized solutions, addressing specific impurity challenges and optimizing carbon capture and storage operations. We provide detailed reports and actionable insights, enabling clients to make informed decisions regarding process improvements, impurity mitigation strategies, and overall efficiency.
As the world shifts towards carbon reduction strategies, the adoption of CCS is likely to become an important priority for CO2 emitters to consider. CleanAir recognizes the significance of accurate measurement and monitoring in ensuring the efficacy of CCS. By leveraging our measurement services, companies can navigate the challenges posed by impurities, maximize carbon storage capacity, and capitalize on financial incentives.